Rotational molding, sometimes referred to as rotomolding, rotomolded, or roto-casting, is an industrial technique for producing hollow parts of any size. The best options for rotational molding are large, single-piece hollow components and double-walled open containers. This is an economical way to make big plastic pieces. A heated, gently rotating mold is filled with resin and rotated vertically and horizontally. Simultaneously heating and rotating, the resin is dispersed and fused on the inside surfaces of the mold. Read More…
As a full-service rotational molding company, Roto Dynamics is your source for high quality, custom rotomolded products. Since our inception, we have continued to earn success by closely working with our customers, developing innovative and tailored solutions. We are with you every step of the way, from design and development to production and assembly. For a complete view of our capabilities and ...
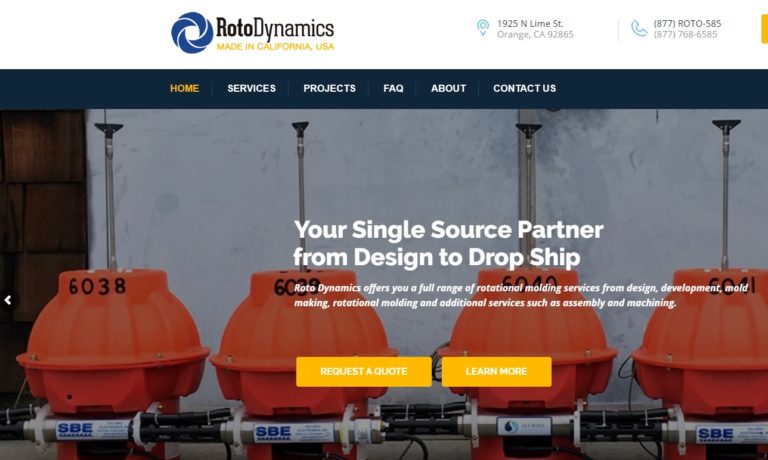
We are a custom manufacturer of rotationally molded products. Our state of the art technology creates precise, cost effective and dependable products. Whether your order is large or small, we want to be sure you are satisfied.
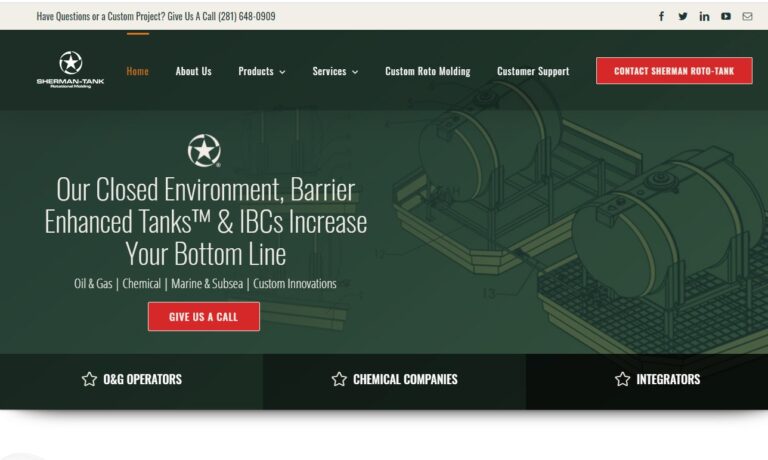
Western Industries Plastic Products, LLC, specializes in large-part plastic blow molding. We provide expertise and services in product design, process improvement, and product assemblies. We offer our customers comprehensive services and turnkey opportunities to achieve their specific project goals. We can assist with: R&D, product design, product improvement, and secondary-fixture design. For...
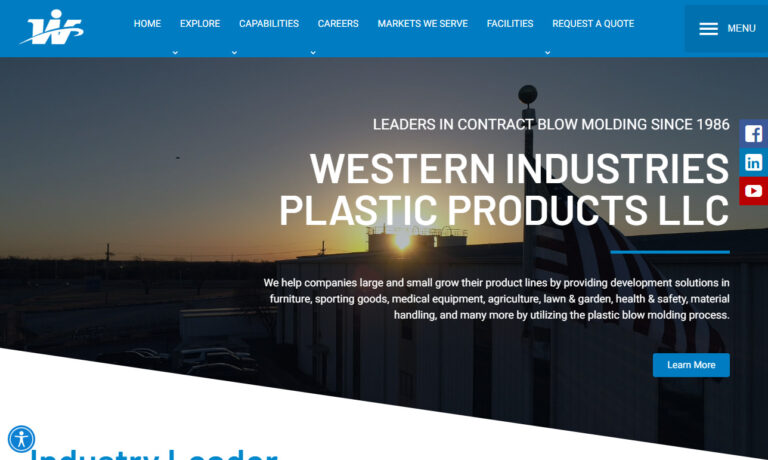
Michiana Rotational Molding provides unparalleled rotational molding services that ensure efficient design, innovation, and functionality. Based in southwest Michigan, the company offers engineering, prototyping, finishing, design consulting, and quality control services. It has experience creating solutions for clients in the marine, home and garden, RV, and material handling industries and more ...
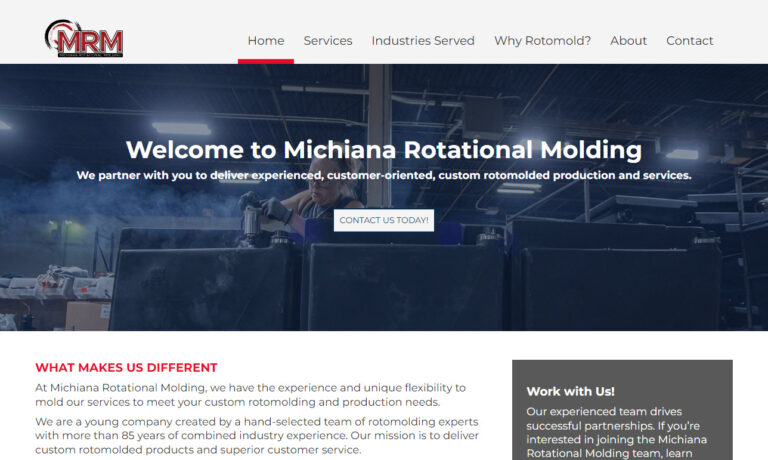
We provide outstanding custom plastic rotational molding. Our teams offer short lead times and we will assist you from concept to production. All of our materials and designs are FDA approved and we can handle the most complex projects. We are your one stop shop for all of your rotational molding needs. Give us a call today to learn more information!
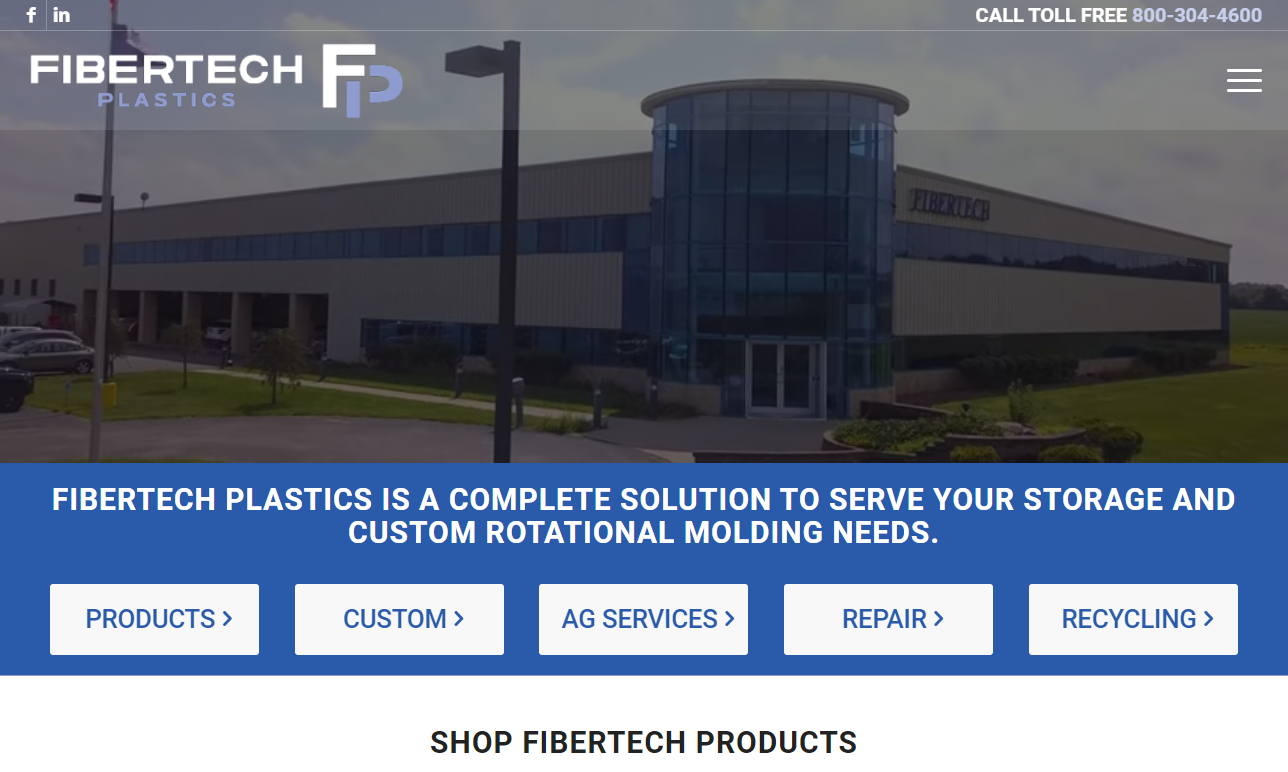
Our warehouses and equipment are designed to protect the quality and condition of the rotationally molded plastic products we sell and process. Our facilities feature state of the art equipment, and are run by a team of dedicated staff members who will help you find what you need. Contact us today!

Here at Hedstrom, we specialize in engineering, designing and manufacturing rotationally molded plastics; chemical and fuel tanks; retail displays; lawn and garden items; medical supplies; recreational, toy, sport and playground objects, plus more. Contact us about your roto molding needs.

At Axisnorth Solutions, we specialize in crafting innovative solutions through our rotational molding, blow molding, and vacuum forming expertise. With a collective commitment to precision and excellence, we bring a wealth of experience to the table. Our seasoned team leverages cutting-edge techniques in rotational molding to produce seamless and durable products. Our meticulous attention to...

More Rotomolding Companies

Rotomolding Process
Hollow object production is done via rotational molding. A preweighted amount of polymer, either in liquid or powder form, is first added to one-half of a cold mold to start the process. Next, the mold is sealed and put inside an oven biaxially rotated. At first, the polymer rotates inside the mold as it spins. Most of the polymer mass remains at the bottom of the mold, forming a pool because of the low rotational speed, which ranges from 2 to 20 rpm.
The polymer starts to melt, or react in the case of thermosets, as soon as the inside surface of the mold reaches a sufficient temperature, coating the mold. As the mold turns, additional polymer layers cover the mold's inner surface until the entire polymer pool disappears. The mold is moved into a chilly area, and the molding is removed once it has cooled to the proper temperature so that a fresh batch of polymer can be charged to start the next cycle.
Rotomolding Products
The industrial potential for items made using rotational molding is practically infinite. The transformation of products composed of less resilient materials into rotomolded products is an increasing trend in manufacturing. Because of the method and the properties of the materials, rotomolding offers a wide range of advantages. Some examples of rotomolding product conversions include pallets, agricultural tanks, drainage piping, laundry carts, Department of Defense items, air cargo containers, burial urns, cemetery products, and even tornado shelters.

Types of Rotomolding Machines
- Rock and roll machine
- Clamshell producer
- Up and over rotational machine
- Material jetting machine
- Shuttle machine
- Swing arm machine
- Carousel machine
The rock and roll machine mostly produces long, narrow pieces. The clamshell machine occupies less area than the shuttle and swing arm machines while still heating and cooling in the same chambers. Due to their modest heating and cooling chambers, vertical rotational machines are small-to-medium in size and energy-efficient compared to the other rotomolding machines.
In addition, although there is a single-arm shuttle machine, most shuttle machines have two arms that alternate the molds between the cooling station and the heating chamber. The arms revolve the molds in a biaxial motion and are independent of one another. Finally, the swing-arm machine is advantageous for businesses with extensive cooling cycles or significant demolding durations. It has a biaxial movement and up to four arms.

Areas Where Rotomolding Can Be Used
Food Sector
Temperature-sensitive food items or dry ice pellets and blocks can be transported and stored in the food business using rotomolded packaging. This is possible, for instance, with an insulated polar container. Rotomolded using foam insulation and FDA-approved polyethylene, polar containers are perfect for the food distribution, fish, and wine industries.
Military Sector
The military sector needs to use high-quality cases to transport its robust equipment. Rotomolded packaging and cases are ideal for handling materials where delicate equipment needs to be transported or stored safely.
Medical Sector
In the medical industry, it is typical to transport and store fragile equipment. Therefore, packaging for medical and pharmaceutical products must adhere to strict standards and rules that often require rotomolded cases.
Advantages of Rotomolding
- Rotational molding has several benefits, including homogeneous wall thickness, minimal tooling costs, and design flexibility. Molds can be made in a wide variety of sizes and shapes. Additionally, there are several choices for textures, colors, and materials using rotomolding. They are economical and environmentally friendly because extra material is frequently reused.
- Rotational molding is superior to other molding techniques in terms of design. With the right design, items that are put together from numerous pieces can be molded as one part, reducing the need for expensive fabrication.
- Other inherent design advantages of rotomolding include constant wall thickness and robust exterior corners that are almost stress-free. Reinforcing ribs can be built into the part to increase strength. These ribs can either be introduced or designed into the component.
Drawbacks of rotomolding
- Slower production time
- Rotomolding uses more plastic, so products are heavier
- The process has a low thermal efficiency, resulting in longer cycles
Choosing the Proper Rotomolding Company
To make sure you have the most productive outcome when selecting a rotomolding company, it is important to compare at least 5 companies using our rotomolding directory. Each rotomolding company has a business profile page that highlights their areas of experience and capabilities and a contact form to directly communicate with the company for more information or request a quote. Review each rotomolding company website using our patented website previewer to get an idea of what each company specializes in, and then use our simple RFQ form to contact multiple rotomolding companies with the same form.